Chimie et explosion : un risque finement calculé
Du fait des produits manipulés, le secteur de l’industrie chimique entretient des liaisons dangereuses avec le risque Atex. Comment améliorer et optimiser la maîtrise des risques liés aux atmosphères explosives ? Examen d’un cas pratique au travers de la mise à jour du DRPCE.
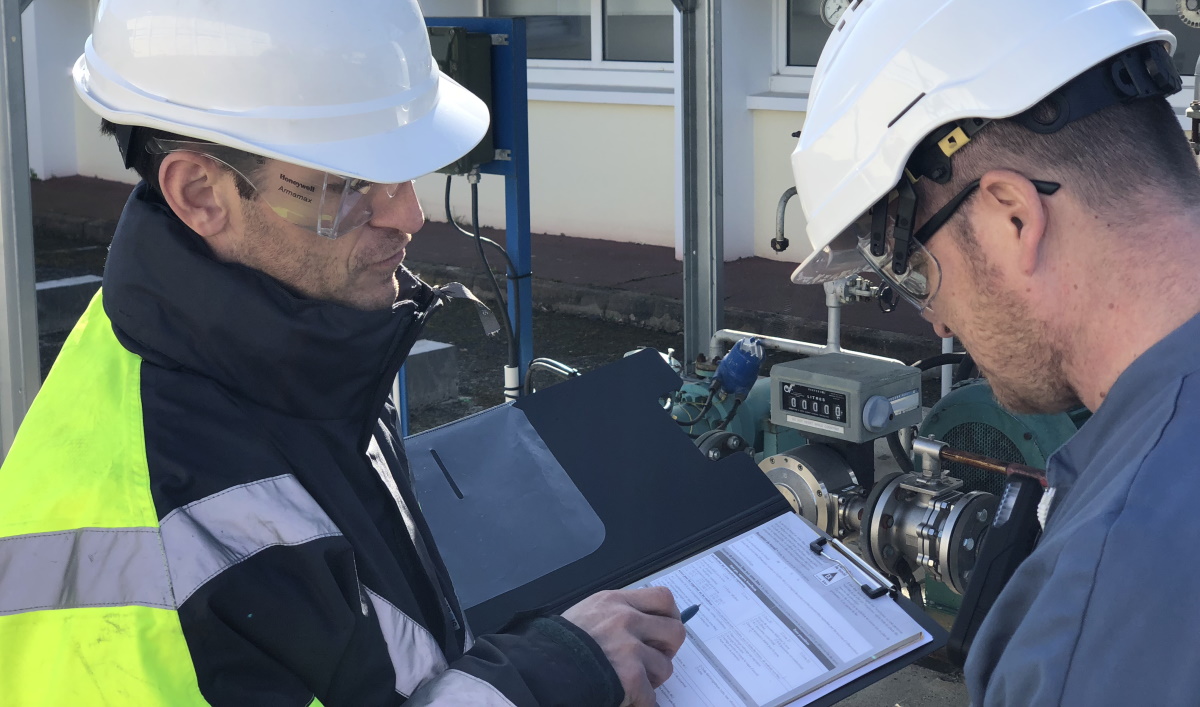
La société Zach System
Installée sur la commune d’Avrillé, dans la périphérie d’Angers (Maine-et-Loire), la société Zach System œuvre dans le secteur de la chimie depuis les années 1970. Filiale du groupe italien Zambon, l’entreprise fabrique des intermédiaires de synthèse et des principes actifs à usage pharmaceutique, à destination humaine ou vétérinaire. Elle réalise également des travaux de recherche et développement visant la mise au point de procédés de fabrication industrielle. De fait, la production peut concerner une dizaine de kilos pour certains composants à plus de 100 tonnes pour certains produits. Les fabrications sont effectuées par campagnes et nécessitent plusieurs opérations successives. Installé sur une surface de 10 ha dont seule la moitié est occupée, le site comprend différents secteurs : des ateliers de production, des unités de stockage, des installations de maintenance, des laboratoires, une partie magasin-logistique et des bâtiments administratifs. Les effectifs de la société avoisinent les 200 personnes.
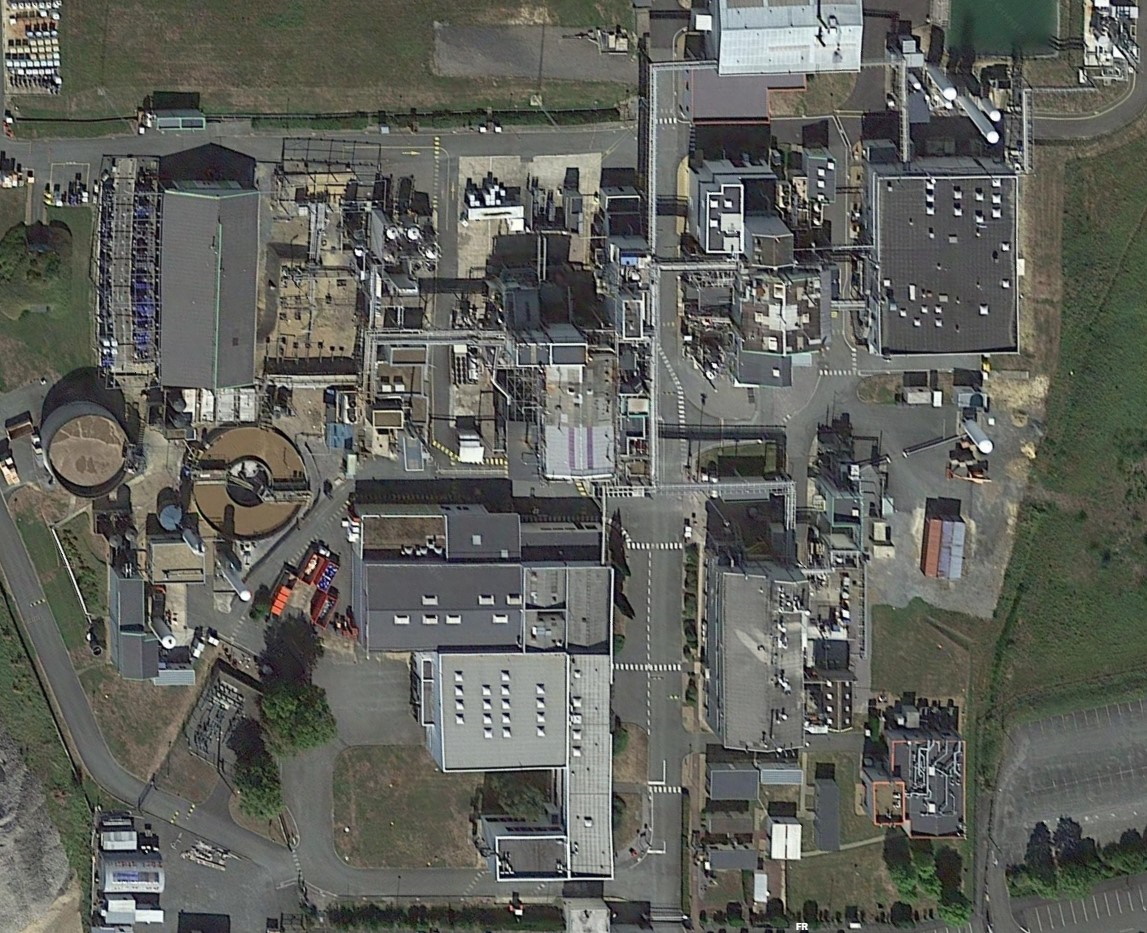
Située à Avrillé, non loin d’Angers, Zach System est une entreprise chimique classée Seveso seuil haut.
Réparties sur 5 ha, ses installations comportent un certain nombre de zones Atex.
Mise à jour du DRPCE
Classé Seveso seuil haut, le site d’Avrillé a la particularité de combiner des activités de chimie fine (réacteurs, filtres sécheurs…) et d’industrie pharmaceutique (broyeurs, atomiseurs, mélangeurs…). L’exploitant est donc sujet aux Atex selon la double problématique gaz-vapeurs et poussières. Plus précisément, des zones comme les ateliers de production et les zones de stockage peuvent présenter une atmosphère explosive gaz-vapeurs par la présence de gaz inflammables et de liquides inflammables. Tandis que les ateliers de produits finis sont exposés aux Atex par les poussières combustibles.
La volonté de Zach System a été de réexaminer ses risques d’explosion au travers de la mise à jour du DRPCE, le Document relatif à la protection contre les explosions. Le DRPCE est intégré au Document unique d’évaluation des risques professionnels (DUERP). Morgan Emzivat, ingénieur HSE, nous explique les motivations de la révision de ce document : « L’objectif était de réévaluer le risque explosion avec un expert tiers. Un expert nous fait profiter de ses compétences et de son expérience. D’autre part, rien ne vaut un oeil extérieur à l’entreprise pour prendre du recul. » Au terme d’un appel d’offre, c’est CNPP qui a été choisi pour effectuer la mise à jour du DRPCE. « Nous avons voulu ré-identifier les zones d’atmosphères explosives grâce à la méthode Evarex proposée par CNPP, donc revoir notre zonage avec une perspective d’optimisation. Une autre volonté était de sensibiliser nos salariés au risque Atex, poursuit le représentant de Zach System. Ce sont des actions qui se font au long cours, dans la durée. On avait aussi l’ambition de travailler sur la révision du DRPCE en mode projet, en associant le tiers expert, l’équipe HSE, des personnels de production et des équipes techniques. »
Le classement des zones Atex
La pierre angulaire pour une bonne évaluation du risque est de se baser sur un classement de zone le plus juste possible. Pour cela, la sélection de la méthode de classement de zone peut faire appel aux guides professionnels, aux normes dédiées aux installations spécifiques (locaux de charges, cabine de peinture…) ou aux normes internationales pour le classement de zone Atex (pour les gaz et vapeurs NF EN 60079-10-1 et pour les poussières combustibles NF EN 60079-10-2).
L’application de ces référentiels conduit à la classification des zones d’atmosphère explosive d’un site selon trois types. C’est le « zonage » :
- zone où l’Atex est présente en permanence, pendant de longues périodes ou fréquemment (0 ou 20) ;
- zone où l’Atex se présente occasionnellement en fonctionnement normal (1 ou 21) ;
- zone où l’Atex n’est pas susceptible de se présenter en fonctionnement normal, ou n’est que de courte durée (2 ou 22).
La norme EN 600079-10-1, établie sur des formules mathématiques permettant de calculer des taux de dégagement de vapeurs-gaz inflammables et sur des ventilations, a été mise à jour en 2016 et est entrée en application
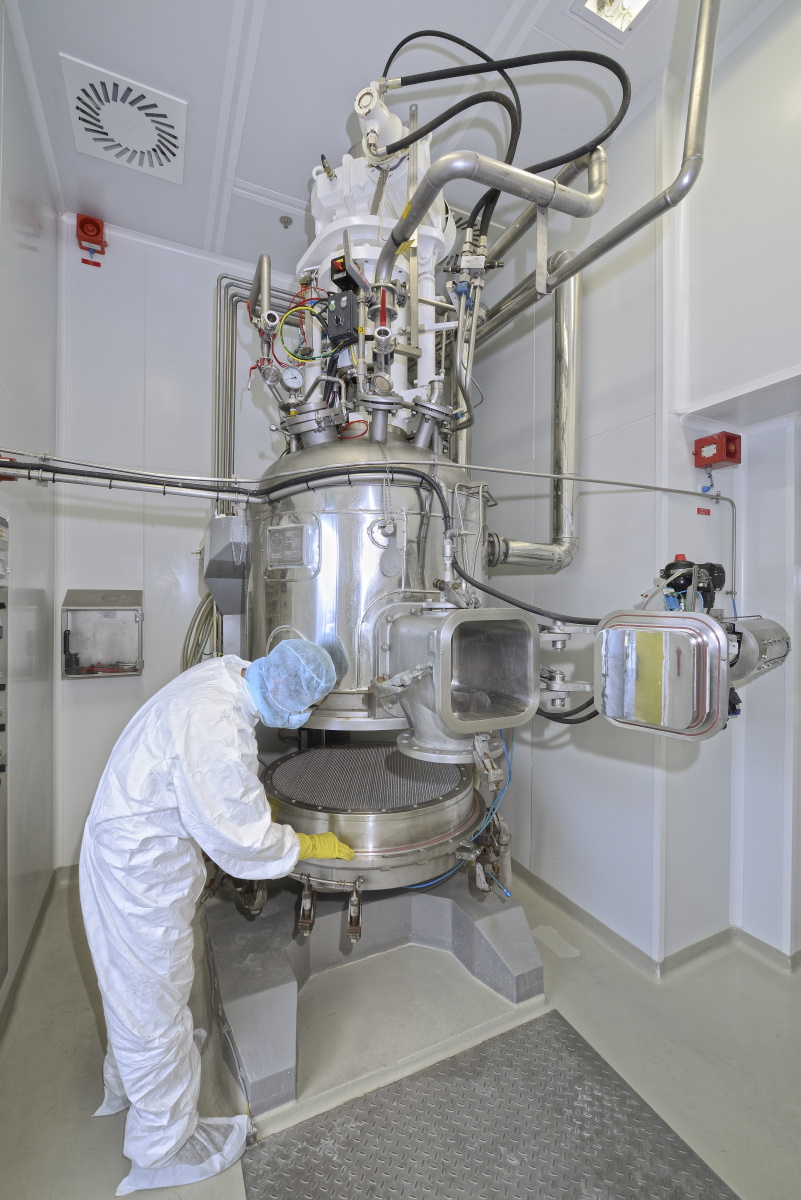
Un opérateur intervient sur un filtre sécheur. La particularité de cet équipement est d’être concerné par la double problématique Atex gaz/vapeurs et poussières. L’inertage et la mise à terre sont certaines des mesures prises pour éviter la formation d’étincelle.
Crédit: Olivier Calvez/Zach System.
l’année dernière (harmonisée au titre de la directive Atex). Plus fine, cette nouvelle version permet, dans certains cas, de réduire le niveau de classement de la zone Atex et son étendue. Ce qui intéresse évidemment l’industriel, puisque cela permet d’optimiser le traitement du risque.
Zonage et optimisation
L’évaluation des risques par la méthode Evarex (lire ci-dessous) sur le site de Zach System a pris son point de départ dans l’identification des zones Atex, leur classification et leur dimensionnement. Ce nouveau zonage a-t-il permis de révolutionner le classement initial ? Pour reprendre les termes de l’ingénieur HSE de l’entreprise : « Ça n’a pas été une révolution. Typiquement, pour un réacteur, le zonage n’a pas été impacté. En revanche, pour nos zones de stockage, la classification a pu évoluer. En termes de hauteur par exemple, en tenant compte de la ventilation, on a pu optimiser le classement. »
Optimiser le classement Atex s’entend par le déclassement d’une zone vers une zone moins dangereuse, la création d’une zone moins dangereuse au sein d’un zonage initial ou la réduction du dimensionnement d’une zone. L’optimisation s’obtient en jouant sur un paramètre permettant de réduire le risque de formation d’atmosphère explosive. C’est généralement la ventilation pour les gaz et vapeurs, mais ça peut être aussi la température des fluides manipulés ou celle du local considéré. Concernant l’Atex poussière, on intervient généralement sur l’aspiration et le dépoussiérage.
Cette optimisation est intéressante pour l’exploitant, à plusieurs titres. Financièrement tout d’abord, dans le cas où les modifications demandées n’exigent que des investissements mineurs (augmenter la ventilation, nettoyer les filtres plus régulièrement, etc.). Les besoins d’équipement en matériel Atex spécifique (la conformité des matériels s’entend par rapport à la zone spécifiée) peuvent également être optimisés. Que ce soit du point de vue du choix du matériel Atex, de son installation ou de sa maintenance. En termes organisationnels, l’optimisation entraîne une simplification des interventions. Ainsi les procédures sont allégées (permis de feu), les besoins en formation du personnel plus ciblés. La signalétique est adaptée en conséquence.
Audit du matériel
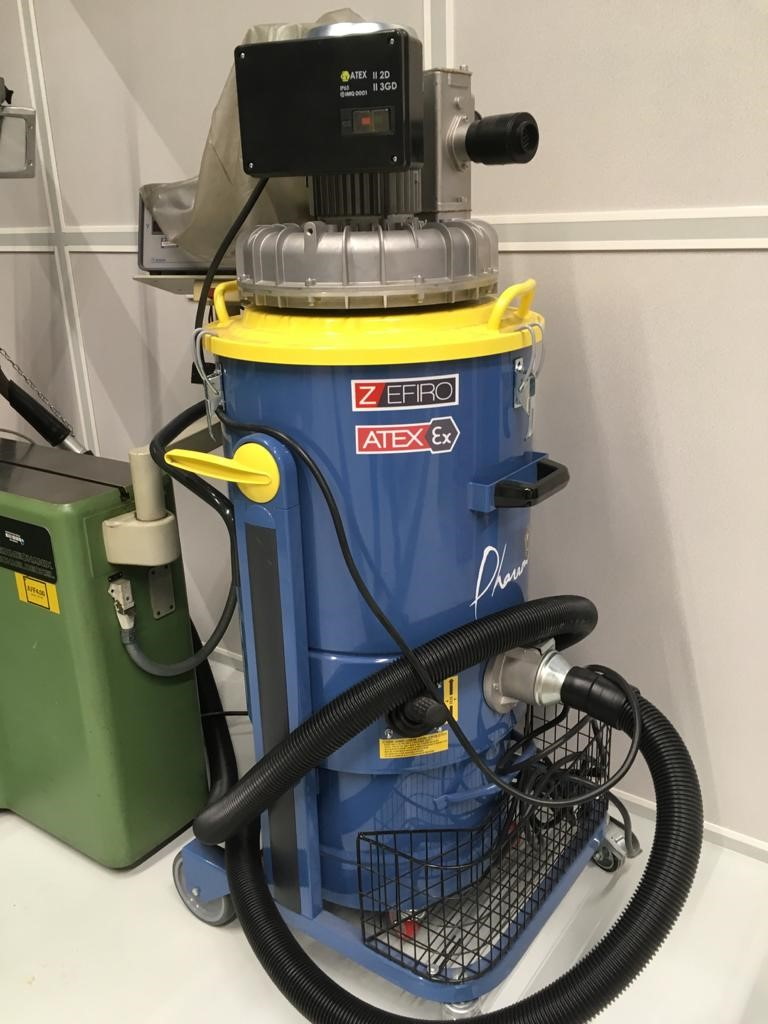
Les matériels électriques et non électriques installés ou susceptibles de pénétrer dans les zones Atex, comme cet aspirateur, doivent être conformes aux prescriptions techniques liés aux types de zones. Un marquage spécifique sur l’appareil permet d’identifier ses caractéristiques.
Parallèlement au zonage Atex du site, il est important de s’assurer de l’adéquation des matériels électriques et non électriques présents ou entrant dans ces zones. Car c’est en grande partie de ces matériels que dépendent les sources d’inflammation potentielles. Parmi ces dernières, on notera ainsi les surfaces chaudes (moteurs, frottement des pièces…), les flammes et gaz chauds (soudage, découpage…), les étincelles d’origine mécaniques (friction, choc, abrasion…), le matériel électrique, l’électricité statique, la foudre ou certaines ondes électromagnétiques radiofréquences (téléphones, radio émetteurs…).
Chez Zach System, il s’agit d’un travail au quotidien, qui a fait l’objet d’un audit par un expert de CNPP. « Sur les bases de cet audit, poursuit Morgan Emzivat, on a classé les remarques par ordre de priorité en fonction de la dangerosité de la situation. Ça permet à nos équipes d’avancer avec un cadre hiérarchisé, et donc d’être efficaces. »
Former l’humain
Un zonage affiné et un matériel expertisé constituent les bases d’une étude Atex. En revanche, il est fondamental de ne pas négliger le facteur humain dans l’équation. Le retour d’expérience en matière d’explosion enseigne que souvent, comme en matière de catastrophe aérienne, le maillon faible provient de l’opérateur. C’est d’ailleurs la raison pour laquelle les inspections des installations classées mettent de plus en plus l’accent, à côté du zonage et de la conformité du matériel, sur la gestion du facteur humain. Les axes d’amélioration sont nombreux et doivent être orientés tant vers le personnel interne que vers les sous-traitants. La rationalisation des process de production y participe, en évitant les manipulations dangereuses pouvant conduire à la création de sources d’inflammation. En cas de travaux ou phases de travail spécifique comme la mise à l’arrêt/redémarrage des installations, une autorisation de travaux en zone Atex doit être mise en place.
Enfin, la formation est un axe fort, ce qu’a bien compris Zach System : « En plus de notre démarche de formation et de sensibilisation de nos salariés et de nos prestataires au risque explosion, on essaie de mettre en place des bonnes pratiques. Nous allons ainsi attirer l’attention de notre personnel de maintenance sur le zonage Atex. On n’installe pas un matériel Atex n’importe comment, il faut suivre la notice scrupuleusement. »
Le secteur de l’industrie chimique est propice à la formation d’atmosphères explosives. Zach System, spécialiste en chimie fine et experte en manipulations de molécules complexes, a adopté une attitude comparable dans le traitement du risque d’explosion. Fallait-il en douter ?
Article extrait du n° 560 de Face au Risque : « Atex : éviter l’explosion » (mars 2020).
Bernard Jaguenaud – Rédacteur en chef
Les plus lus…
Dans un flash Aria daté de juillet 2025, le Bureau d’analyse des risques et des pollutions industrielles (Barpi) rappelle l’importance…
L'entreprise Blue Solutions, filiale du groupe Bolloré, a répondu aux accusations de l'entreprise Highway France Logistics 8, propriétaire de…
Deux décrets ainsi qu’un arrêté, tous trois en date du 11 juin 2025, portent sur les règles de sécurité incendie…
Ce numéro 608 du magazine Face au Risque (juillet - août 2025) consacre un dossier spécial à la vidéosurveillance…
Un décret publié au Journal officiel le 27 juin 2025 et entré en vigueur le 1er juillet élargit les zones…
L’AFCDP (Association française des correspondants à la protection des données) annonce la publication du livrable du groupe de travail…