Réfrigération à l’ammoniac : pas sans risques
Le Barpi (Bureau d’analyse des risques et pollutions industriels) a mis à jour son étude sur l’accidentologie des sites utilisant le refroidissement à l’ammoniac. Si une stagnation des événements est noté, il n’en reste pas moins qu’il existe une marge d’actions pour les réduire.
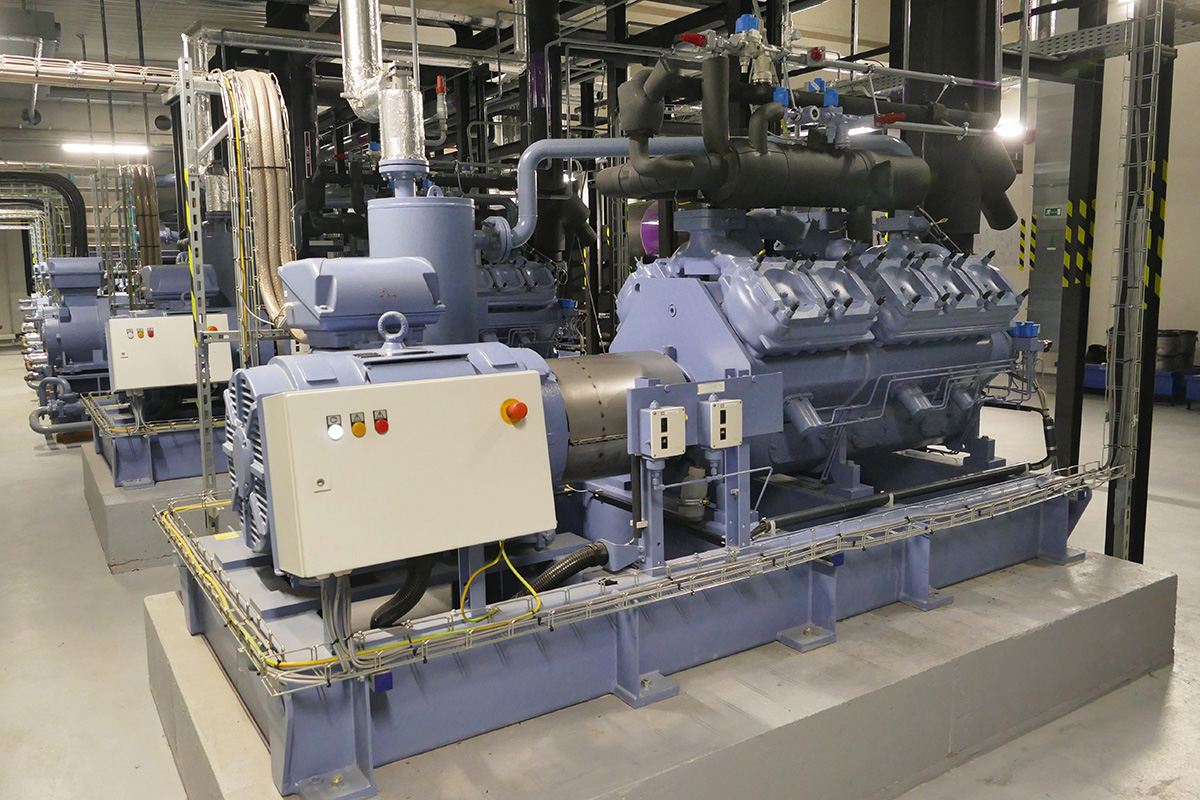
Un produit très courant
L’ammoniac, gaz parmi les plus synthétisés au monde et connu depuis l’antiquité, est utilisé dans la réfrigération. L’ammoniac est comprimé pour être rendu sous une forme liquide nécessaire à son utilisation en tant que réfrigérant.
L’ammoniac a été utilisé durant des décennies dans la réfrigération pour ses excellentes propriétés thermodynamiques. Puis il a été progressivement remplacé, à partir des années 1970, par les gaz réfrigérants chlorofluorocarbonés (CFC), moins performants thermiquement mais moins toxiques. Dans les années 1990, suite à la signature du protocole de Montréal en 1987 visant à interdire l’utilisation des CFC, l’ammoniac est revenu peu à peu au premier plan. Il est attendu une nouvelle évolution de son utilisation suite à l’interdiction progressive des HFC depuis le 1er janvier 2020.
L’utilisation de l’ammoniac en réfrigération implique de respecter la réglementation relative aux appareils à pression ainsi que, si les quantités utilisées dépassent 150 kg, la réglementation relative aux ICPE (rubrique 4735 de la nomenclature).
Le Barpi a mis à jour les deux précédentes synthèses ammoniac datant de 1995 et 2002.
L’accidentologie sur les neuf dernières années montre une stabilité relative autour de 11,6 événements par an (écart type de 2,5). L’agroalimentaire, particulièrement les abattoirs et les laiteries/usines de transformation du lait, est le secteur le plus représenté.
En raison de ses propriétés toxicologiques, les événements mettant en cause l’ammoniac ont des conséquences humaines dans 16 % des cas dans les ICPE, causant notamment des brûlures et des intoxications. Les événements impliquant l’ammoniac nécessitent le confinement ou l’évacuation des riverains dans 27 % des cas.
Fiche d’identité de l’ammoniac
Seuils toxicologiques | Danger |
---|---|
SELS (60 mn) : 3 633 ppm SPEL (60 mn) : 3 400 ppm SEI (60 mn) : 354 ppm |
H221 : Gaz inflammable (catégorie 2) H280 : Gaz sous pression H331 : Toxicité aiguë, par inhalation (catégorie 3) H314 : Corrosion cutanée (catégorie 1B) H400 : Danger pour le milieu aquatique – danger aiguë (catégorie 1) |
Les dangers de l’ammoniac
L’ammoniac est nocif par inhalation et mortel à haute dose. En cas de contact, il provoque de graves brûlures de la peau et des lésions oculaires. Il attaque le cuivre et tous ses alliages, ainsi que le zinc. Ainsi, les installations frigorifiques fonctionnant à l’ammoniac sont réalisées avec des tuyauteries en acier.
Des rejets en quantités importantes
95 % des événements recensés sont des rejets, 13 % des incendies. Les quantités d’ammoniac rejeté ne sont connues que dans la moitié des événements. Les rejets d’une tonne et plus représentent encore plus de 10 % des événements (voir graphique ci-contre).
Répartition des quantités connues d’ammoniac rejeté accidentellement
200-999 kg
30 %
≥ 1000 kg
12 %
< 100 kg
30 %
100-199 kg
27 %
« Dans 16 % des cas, les événements mettant en cause l’ammoniac ont des conséquences humaines causant brûlures et intoxications. »
Les défaillances matérielles
Elles représentent près de 70 % des causes premières. Elles sont suivies des opérations de maintenance sur le matériel avec 18 % des cas et les montées en pression des installations de réfrigération menant à l’ouverture d’une soupape dans 10 % des cas (voir graphique ci-contre).
Nota : les défaillances sur les soudures en lien avec un organe ne sont pas comptabilisées dans l’organe en question.
Ces éléments montrent l’importance :
Nombre de défaillances
constatées par organe
En % sur 37 événements
- de maîtriser les interventions sur les installations de réfrigération, qu’elles soient réalisées en interne ou par un prestataire externe ;
- de réaliser une maintenance attentive sur les équipements composant ces installations de réfrigération.
Tuyauterie rompue peu après la bride et vue du caisson à la sortie du refoulement du compresseur d’ammoniac (site chimique).
Rupture d’un piquage, retrouvé sur le sol, dans une boulangerie industrielle.
Des causes profondes trop peu souvent recherchées
En effet, celles-ci, qui comprennent les facteurs organisationnels et humains, n’apparaissent dans les rapports d’analyse que dans 60 % des cas.
Dans les événements où les causes profondes ont été recherchées, l’organisation des contrôles est en cause dans 9 cas sur 10, suivie de problèmes d’ergonomie dans 15 % des cas.
Des pistes à suivre
L’analyse des événements montre que ces installations demandent une compétence sans faille pour les concevoir, les maintenir et les exploiter. Cela implique la mise en place de dispositifs de sécurité ainsi que des procédures opérationnelles pouvant être contraignantes.
Les exploitants doivent par exemple :
- mettre en place un contrôle et une maintenance effective et adaptée des installations afin d’éviter les problèmes matériels ;
- mener une analyse de risques préalable, mettre à disposition des procédures adaptées et définir clairement les actions à mener en cas de fuite d’ammoniac, afin d’accompagner au mieux les opérateurs lors des opérations de maintenance ou de travaux. Il est important d’assurer une surveillance et un contrôle de bonne réalisation de ces opérations, y compris les opérations sous-traitées ;
- mener une réflexion sur les choix de matériel, de leur configuration, ou de leur implantation au regard de la prévention des risques afin de réduire les conséquences des événements. Cette réflexion doit intégrer le volet « ergonomie ».
Les accidents emblématiques
En savoir plus
Retrouvez la synthèse ammoniac sur le site internet du Barpi.
Article extrait du n° 597 de Face au Risque : « Construction bois et sécurité incendie » (novembre 2023).
Vincent Perche
Responsable de la cellule chimie, informatique et équipements sous pression du Barpi (Bureau d’Analyse des Risques et Pollutions Industriels)
Les plus lus…
Les nouvelles obligations introduites par un décret et un arrêté du 27 mai 2025 pour protéger les travailleurs contre…
Le lundi 23 juin, les 27 États membres du Conseil de l’Union Européenne ont trouvé un accord pour simplifier…
Un arrêté du 24 juin 2025, publié au Journal officiel du 26 juin, porte approbation des règles de sécurité…
Un arrêté du 12 juin 2025, publié au Journal officiel le 26 juin, modifie les prescriptions applicables aux stockages…
Le salon APS se tiendra du mardi 7 au jeudi 9 octobre 2025 au Parc des expositions, situé à…
C’est parti ! Vous pouvez dès maintenant demander votre badge pour le Salon APS 2025, le rendez-vous expert de la…